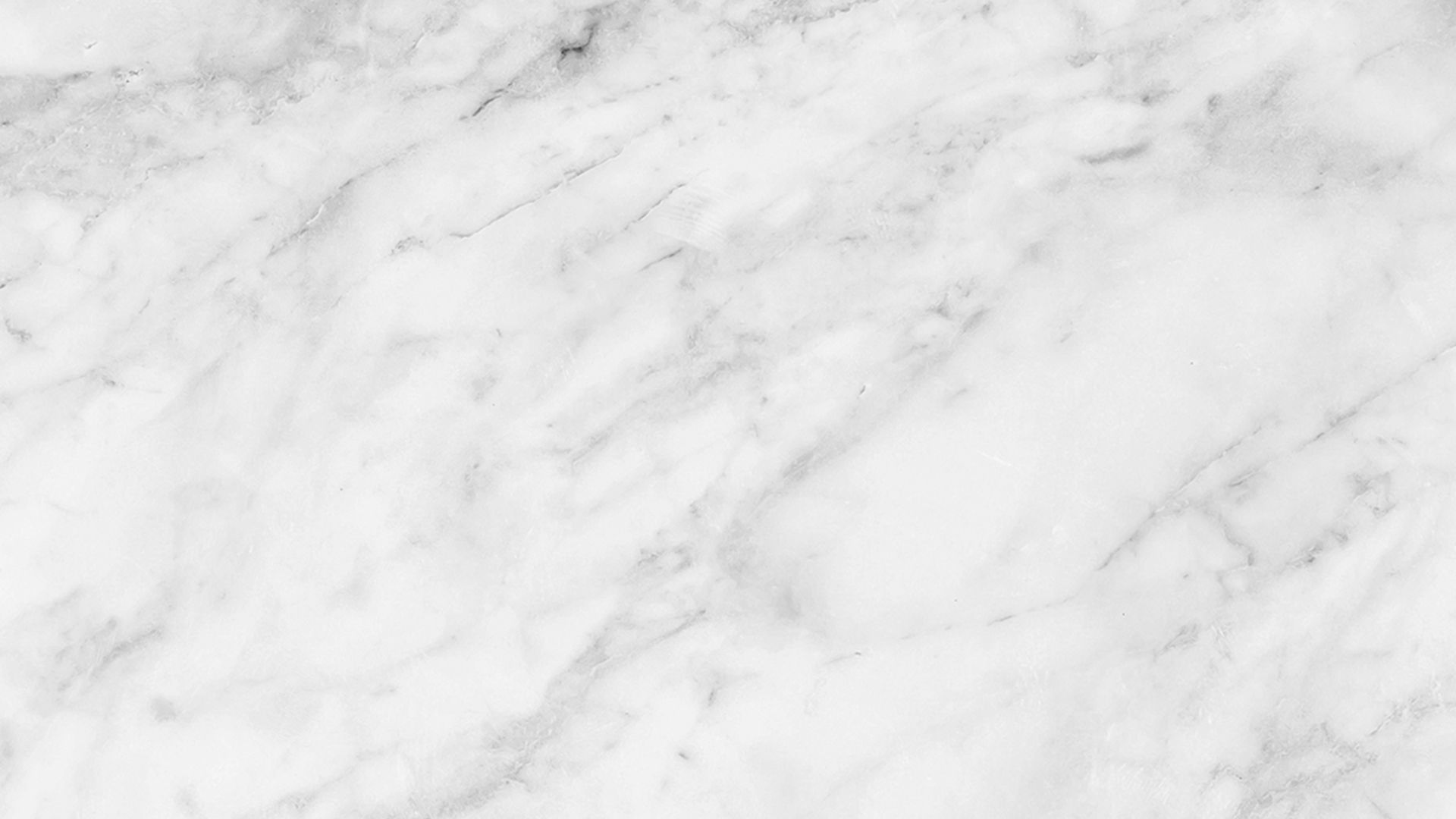
Gunjan Agarwal
PhD, Mechanical Engineering
Massachusetts Institute of Technology (MIT)









Automotive: Crashworthiness and Occupant Safety
Affiliation: Tesla Inc.
Groups: Computer-Aided Engineering, Vehicle Test Engineering
-
Driving numerical simulations, mechanical design and structural optimization to enhance vehicle safety.
-
Safety performance of the vehicle is evaluated in terms of:
-
Crashworthiness: Improved response to all possible vehicle crash modes - Full Frontal, Frontal Offset Deformable Barrier, Side Pole, Side Moving Deformable Barrier, Oblique Impact, Rear Impact, Roof Crush and Rollover.
-
Occupant Safety – Different occupant statures - Hybrid III 5th percentile female, 50th percentile male, 95th percentile male, 6 year and 10 year old child; as well as different seating positions within the vehicle environment, in addition to pedestrian protection collision cases including head impact, lower leg impact, upper leg impact as well as pedestrian detection using passive safety methods.
-
Designing vehicle to excel in multiple international safety standards and new car assessment programs with the highest ratings in:
-
Legal Homologation (e.g. FMVSS - Federal Motor Vehicle Safety Standards in USA, United Nations ECE Economic Commission for Europe regulations in Europe).
-
Customer-valued rating programs – USNCAP, Euro-NCAP and IIHS (Insurance Institute for Highway Safety).
-
Leading development of full-vehicle numerical simulation models using the Finite Element Method to enable improved and efficient design for safe, robust vehicle components that can withstand highly dynamic impact and loading events, targeted towards crash-worthiness and durability.
-
Enabling accurate prediction of complex mechanical behavior and solving multi-physics problems by implementing multiple modeling, computational, optimization and programming platforms such as LS-DYNA, Abaqus, Ansys, Hyperworks, Digimat, Beta CAE, TOSCA, LS-OPT and Python.

Crash dummy model. Image source: Arup/Oasys LS-DYNA.
Wearables: Soft Robotic Exosuits
Affiliation: Ecole Polytechnique Federale de Lausanne (EPFL), Reconfigurable Robotics Laboratory
Partners: Oculus VR, Menlo Park, CA
Funding Agency: National Centre of Competence in Research (NCCR) Robotics
Collaborators: Laboratory for Multiscale Mechanics Modeling (EPFL)
Open Source Robotic Toolkit: Our work was recently featured in Harvard University's Soft Robotics Design Portal. Find the complete set of open-access models and scripts developed here.
Soft fluidic actuators consisting of elastomeric matrices embedded or reinforced with flexible materials are of particular interest to the robotics community because they are lightweight, affordable and easily customized to a given application. They enable the achievement of safer and flexible interaction in a variety of applications including robotic grasping, wearable systems, versatile locomotion, and biomedical rehabilitation. These actuators can be rapidly fabricated in a multi-step molding process and can achieve combinations of contraction, extension and bending motion with simple control inputs such as pressurized air. By defining motion and force profile requirements, it is possible to embed mechanical intelligence into these soft actuators to achieve the performance requirements with simple tunable control inputs. I employ mathematical tools and new design concepts to improve the performance of these actuators compared to existing designs.
Although the scalability, customizability, and diversity of soft actuators are widely recognized, comprehensive techniques for designing, modeling, and fabricating soft actuators are not in place. In particular, existing mathematical tools for modeling soft actuators lack the level of detail, adaptability, and accuracy necessary to match the versatility of the actuators. Characterizing and predicting the behavior of soft actuators is challenging due to the nonlinear nature of the complex hyperelastic, viscoelastic material used and the large range of motions they produce. I have provided the robotic community with a comprehensive, cohesive, and open-source simulation and design tool for soft actuators using the finite element method (FEM), readily compatible with and extensible to a diverse range of soft materials and design parameters. This design tool can enable the generation of improved predictive models that will help us to rapidly converge on new and innovative applications of these soft actuators.
References:
1. Agarwal, G., Besuchet, N., Audergon, B. and Paik, J., Stretchable Materials for Robust Soft Actuators towards Assistive Wearable Devices. Scientific Reports, 2016. doi: 10.1038/srep34224.
2. Agarwal, G., Paez, L., and Paik, J., Design and Analysis of a Soft Pneumatic Actuator with Origami Shell Reinforcement. Soft Robotics, 2016. doi:10.1089/soro.2016.0023.
3. Moseley, P., Florez, J. M., Sonar, H. A., Agarwal, G., Curtin, W. and Paik, J., Modeling, Design, and Development of Soft Pneumatic Actuators with Finite Element Method . Adv. Eng. Mater., 2015. doi: 10.1002/adem.201500503.



Mechanical Design: Thermal Management for High-Power Microelectronic Devices
Affiliation: Massachusetts Institute of Technology, Microsystems Technology Laboratories
Partners: Raytheon Company, Stanford University
Funding Agency: Defense Advanced Research Projects Agency (DARPA)
Collaborators: IBM
Gallium Nitride (GaN) based microelectronic devices have enabled high performance for radio-frequency (RF) applications. Favorable properties of GaN, such as high dielectric strength, high current density, exceptional carrier mobility, high speed switching and low on-state resistance make GaN-based high electron mobility transistors (HEMTs) much sought after in the semiconductor industry for high performance power devices. However, significant performance degradation is observed in GaN HEMTs as the device temperature increases, due to the high power density concentrated in the active region, thus preventing these devices from achieving their full potential. In view of the several limitations suffered by the existing cooling techniques such as high cost, lack of detailed thermal conductivity and electrical characterization, moderate device performance, and high contact resistance, a low-cost approach for cooling GaN HEMTs fabricated on silicon substrates using microfluidic cooling is being modeled and analyzed in this work.
This approach utilizes liquid cooling of GaN HEMTs through microfluidic channels etched into a silicon substrate. The use of a silicon substrate for the fabrication of GaN electronics not only lowers the cost compared to conventionally used SiC, diamond or sapphire substrates for GaN growth, but also enables the heterogeneous integration of silicon-based CMOS/MOSFET devices with GaN HEMTs. Theoretical modeling for heat management in GaN-based microelectronic devices using microfluidic cooling is done using Finite Element Analysis in COMSOL, and results for temperature distribution are recorded for a system comprising multiple cooling microchannels underneath GaN HEMTs. Cooling efficiency is studied for varying configurations of the microchannels, relative to the orientation of the heat sources in the HEMT. The effect of several parameters, including microchannel geometry, coolant flow rates, and geometry of the cooling stack on the cooling efficiency is also studied. Modeling results show that single-phase microfluidic cooling at the optimal flow rates and system geometry can lower peak temperatures in the GaN HEMTs substantially and increase the performance, reliability and lifetime of these devices. The capability to remove up to 4W/mm of power dissipation using cooling arrangements utilizing single-phase laminar flow of only up to 7 mL/min demonstrated here holds promising potential for implementation in high performance RF systems for power amplifiers, transmission lines and other applications in defense and military. Current effort is focused on fabricating the microfluidic cooling platform designed using these model guidelines, integrating it with GaN HEMT and Silicon MOSFET devices, and studying its cooling performance.
References:
1. Agarwal, G., Kazior, T., Kenny, T., Weinstein, D., Modeling and Thermal Analysis of GaN HEMTs using Microfluidic Cooling. ASME Journal of Electronic Packaging, 2016. doi:10.1115/1.4035064.


Micromanufacturing: Selective Self-Assembly and Contact Mechanics of Deformable Microsystems
Affiliation: Massachusetts Institute of Technology, Micropower and Nanoengineering Group
Funding Agency: National Science Foundation (NSF), Air Force Office of Scientific Research (AFOSR), Pappalardo Graduate Fellowship
Collaborators: Laboratory for Multiscale Regenerative Technologies (MIT), The Doyle Group (MIT)
Bottom-up fabrication techniques such as self-assembly are a very effective means of integrating small-scale building blocks into complex, more valuable architectures, which are difficult to create using conventional, top-down manufacturing methods. This research organizes small-scale components into shape- and size-matched sites on a template’s surface using a novel type of selective assembly: templated assembly by selective removal (TASR). The TASR approach utilizes surface interactions between the components and substrate to promote adhesion and thereby the assembly of the components on the substrate surface. The magnitude of these surface interactions is at its peak value when the shapes and sizes of the components match the shapes and sizes of the assembly sites, and the contact area between interacting surfaces is maximized. The incorporation of fluid forces created by externally-input, high frequency (MHz-range) acoustic excitations makes this technique highly selective in component placement, by dislodging components from any poorly-matched wells in which they may have assembled. Quasi-random assembly and deterministic selective removal proceed until the system is fully assembled. Selectively self-assembled systems are important for a wide range of applications, ranging from metamaterials, MEMS and microelectronics, optically-based chemical sensors, bio-medical diagnostics, to shape- and size-based chromatography.
Successful assembly of silica microspheres using TASR on a silicon template carried out previously [1-2] established that the technique works effectively for assembly of hard materials on a rigid substrate. However, the situation for the assembly of soft materials is more challenging due to the larger deformation experienced in these systems, which in turn influences the degree of shape matching between the component and the template. This work presents the first experimental demonstration of successful, selective assembly of deformable microsystens using TASR. The TASR technique is demonstrated to achieve highly selective organization of deformable, inorganic micro-components (such as polymer colloids, hydrogels) [3] and biological cells [4] onto patterned rigid substrates, as well as with more economical, replicated polymer templates [5]. An extensive range of material combinations at diverse length scales have been successfully assembled using the TASR process, and the assembly of both isotropic (spherical) and anisotropic (cylindrical) components into corresponding patterned assembly sites has been achieved. Since the TASR system is particularly well matched to the length scales for typical optical and biological systems, the successful selective assembly of deformable microsystems using TASR has opened up a host of applications not previously possible using this technique.
A quantitative mechanical model is also formulated for predicting the degree of success in self-assembly of deformable materials at small scales. Self-assembly depends on the tendency of systems to minimize their free energy. The introduction of either deformable substrate templates or deformable components introduces a new set of considerations, since deformation can change the degree of shape matching between component and substrate, and hence, may change the assembly yield depending on how well the undeformed component matches the undeformed assembly site. Here, an energy-based theory is introduced to model the self-assembly process that takes into account the mechanical behavior of the components and substrate. If the deformations of components and substrate are fully elastic upon interaction, any reduction in system free energy due to the increase in contact area upon deformation will equal the increase in system free energy due to the storage of elastic energy in the deformed structures. Therefore, for purely elastic deformations, the self-assembly is predicted to be successful. In contrast, if the deformation enters the plastic regime, some of the energy will be dissipated, and the assembly process may be marginally successful at best. In that case, the probability increases that deformable components will remain assembled in poorly matched sites from which identically shaped rigid components would have been removed by the selective removal process.
References:
-
S. Jung and C. Livermore, Achieving Selective Assembly with Template Topography and Ultrasonically Induced Fluid Forces, Nanoletters, 2005, 5(11), 2188-94.
-
F. Eid, S. Jung, C. Livermore, Templated assembly by selective removal: simultaneous, selective assembly and model verification, Nanotechnology, 2008, 19, 285602.
-
G. Agarwal, A. Servi, F. Eid, and C. Livermore, Selective Self-Assembly of Polymer Structures using Templated Assembly by Selective Removal, IEEE Transactions on Nanotechnology, 2011, 10(3), 617-625.
-
G. Agarwal, and C. Livermore, Chip-Based Size-Selective Sorting of Biological Cells using High Frequency Acoustic Excitation, Lab on a Chip, 2011, 11(13), 2204-2211.
-
G. Agarwal, and C. Livermore, Size-Selective, Biocompatible, Manufacturable Platform for Structuring Deformable Microsystems, Lab on a Chip, 2014, 14(17), 3385-3393.


